Discover our latest news and impact stories
Stay informed with the latest updates, media coverage, and success stories shaping Nuventura’s journey toward innovative energy solutions.
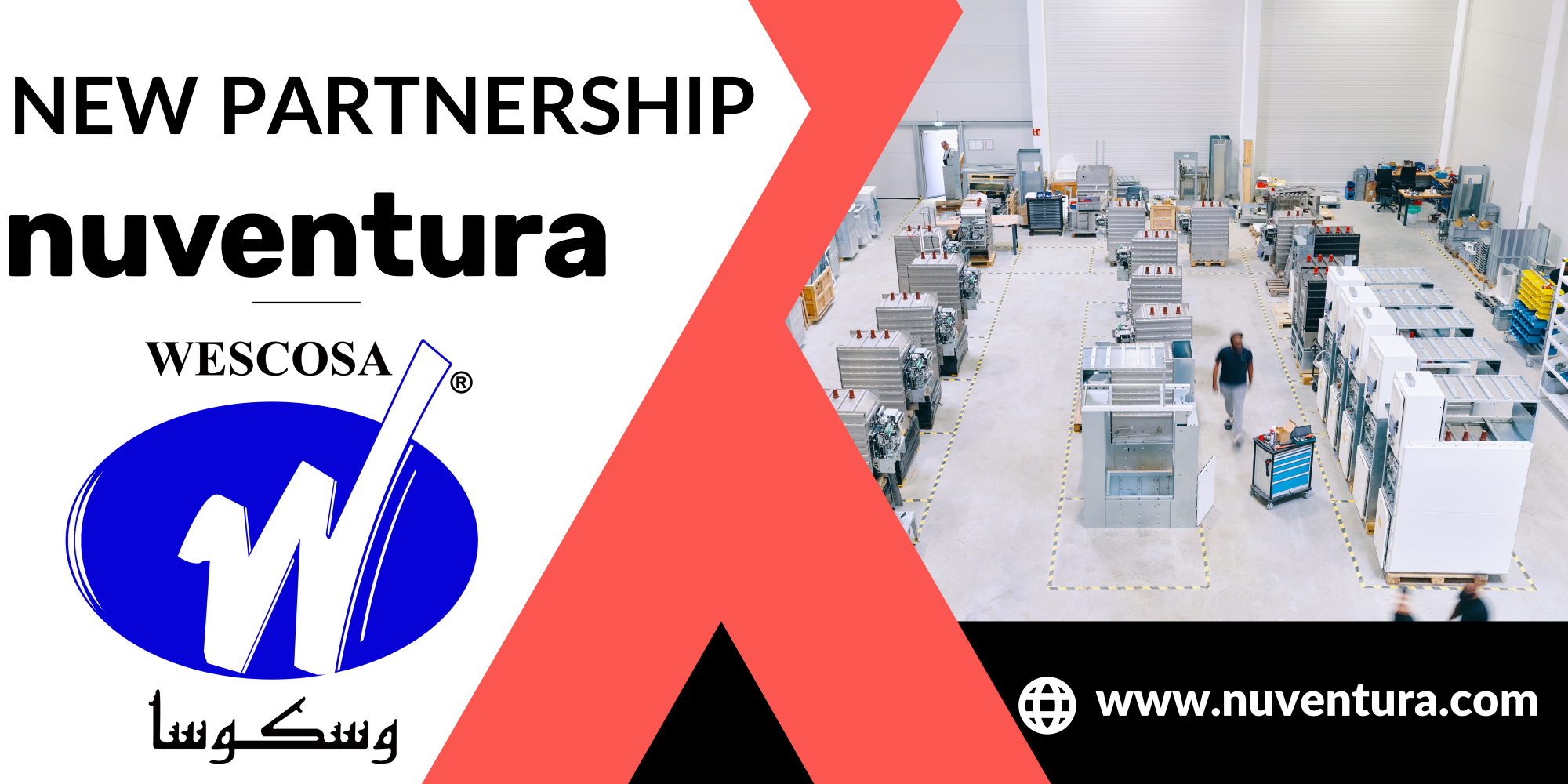
Nuventura and WESCOSA join forces to bring F-Gas-free GIS to the Middle East
We’re thrilled to officially announce our partnership with WESCOSA (Wahah Electric Supply Company of Saudi Arabia Ltd.), a leading switchgear manufacturer based in Saudi Arabia.
More News Posts
No items found.
Nuventura on video
Nuventura media coverage
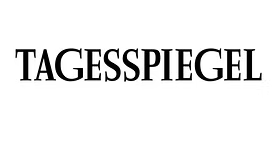
25 Millionen Euro eingesammelt: Berliner Start-up Nuventura will Stromnetz von Klimakiller-Gas befreien
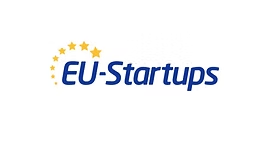
Berlin-based Nuventura secures €25 million Series A to ditch greenhouse gas for good
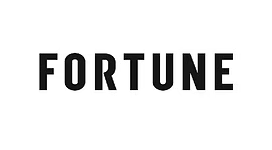
How founders can prepare for the fall fundraising marathon
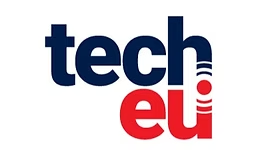
Berlin's Nuventura raises €25M for SF6-free switchgear technologies
Stay informed and inspired
You can also stay informed and inspired by subscribing to our quarterly newsletter
Connect with our experts
Whether it’s SF₆-free switchgear specifications, partnership opportunities or support – our team is ready to answer your questions and find the right eco-friendly solution for your needs.
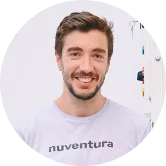